Air conditioning is a staple in Australian homes, especially during the long, hot summers — but many homeowners still face performance issues, rising energy bills, or early system failures. Mistakes such as choosing the wrong unit size or skipping professional advice can seriously affect how well your system cools your home and how long it lasts. On the Central Coast, where coastal humidity and temperature swings are part of daily life, an efficient and well-installed system is essential for both comfort and home protection.
Understanding the most common air conditioning errors — from poor sizing to risky DIY fixes — helps homeowners avoid unnecessary costs and discomfort. The sections below highlight four key mistake areas, explain why they happen, and offer practical ways to avoid them, ensuring your system runs smoothly for years to come.
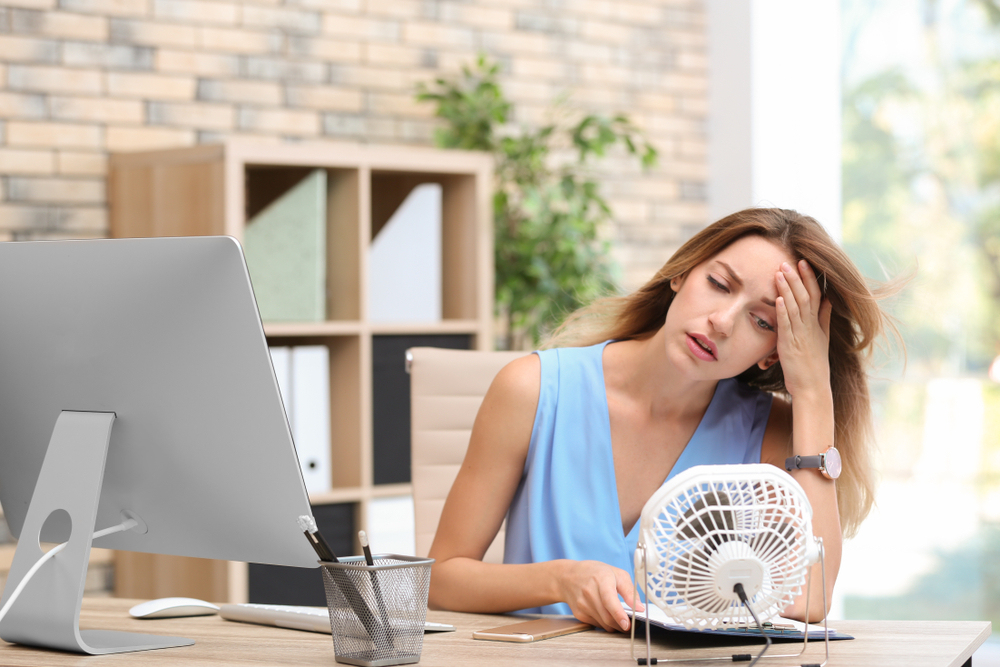
Choosing the Wrong Size System
Selecting equipment that is either too large or too small for the intended space can lead to significant comfort issues and unexpected expenses. A mismatch between capacity and demand affects not only temperature consistency but also humidity control, noise levels, and component lifespan. Careful assessment of dwelling dimensions, insulation quality, and anticipated usage patterns is essential to ensure the chosen system performs as intended.
Oversized Cooling Equipment
Installing a unit with a capacity far exceeding the actual load requirements might seem like a surefire way to stay comfortable, but it introduces its own set of challenges. Excess cooling power causes the system to cycle on and off rapidly, preventing proper moisture removal and driving up wear on components. Such frequent start-stop sequences also disrupt temperature uniformity across different rooms.
Short Cycling of the System
Rapid on-off operation places undue stress on mechanical parts, increasing the risk of compressor failures and reducing overall service life. Each startup consumes a surge of electricity far exceeding steady-state running, driving up power bills. Over time, repeated cycling may necessitate early replacement of critical elements, negating any perceived benefit of extra capacity.
Inadequate Humidity Control
When cooling capacity overshoots demand, the system cools the air too quickly and shuts off before removing sufficient moisture. As humidity levels remain high, occupants may experience clamminess and mould growth despite seemingly cool temperatures. Persistent dampness can also damage interior finishes, upholstery, and fabrics, leading to additional maintenance costs.
Uneven Temperature Distribution
An oversized unit may satisfy the thermostat in one zone and shut down before other areas reach the setpoint, creating hot and cold spots. This inconsistency encourages occupants to adjust vents or increase fan speeds, further complicating airflow dynamics. The result is a persistently unsatisfactory environment that frustrates residents and masks the true cause of discomfort.
Higher Initial and Operating Costs
Larger equipment carries a premium purchase price and can require more robust ductwork, reinforcement, or structural modifications. Even if energy-efficiency ratings are high, the surplus capacity tends to run inefficiently at part load, inflating monthly bills. Over the lifespan of the installation, the cumulative excess energy usage often eclipses the upfront savings from any promotional discounts.
Undersized Cooling Equipment
Conversely, choosing a unit with insufficient capacity forces the system to run continuously in an attempt to achieve the thermostat setting, resulting in poor temperature control and accelerated wear. Constant operation can lead to overheating of components, refrigerant pressure imbalances, and electrical strain. Occupants may also resort to tampering with controls, reducing system reliability even further.
Struggling to Maintain Set Temperatures
An undersized solution fails to lower room temperatures on time, leaving inhabitants feeling persistently warm. The thermostat may read that the desired temperature has been reached, yet the occupied zones continue to feel uncomfortable. This disconnect between gauge readings and real-world conditions often leads to misguided troubleshooting efforts.
Increased Noise Levels
As the system works overtime, fans and compressors labour under continuous load, producing elevated noise that can disrupt rest and daily activities. Prolonged high-speed operation also causes vibration issues, which may loosen mounting hardware and accelerate component fatigue. Over time, noise complaints often reveal underlying capacity mismatches rather than simple mechanical faults.
Reduced Equipment Longevity
Continuous operation without adequate rest periods strains motors, bearings, and electronic controls, hastening component failure. An overworked compressor, in particular, may suffer from lubrication breakdown and overheating, leading to costly repairs or premature replacement. The cumulative damage from always-on service can shorten the expected lifespan by years.
Elevated Energy Consumption
Running at near-maximum capacity for extended periods draws substantial electricity, inflating utility bills beyond anticipated levels. Even highly efficient units lose their advantage when operated continuously at peak load. The long-term financial impact can outweigh the initial savings from selecting a lower-cost, underpowered option.
Failing to Account for Future Needs
A sizing calculation based solely on current conditions neglects potential changes in household occupancy, layout modifications, or insulation upgrades. Without considering future scenarios, the system may become inadequate or overly large after renovations, additions, or shifts in residents’ patterns. Early planning ensures the installation remains suitable for years to come.
Underestimating Occupancy Changes
An increase in household members or frequent gatherings adds a heat load that the original design may not accommodate. Body heat, appliances, and lighting contribute significantly to the total cooling requirement, especially in open-plan layouts. Planning for occasional higher loads prevents discomfort when entertaining or expanding the family.
Ignoring Potential Home Extensions
Planned additions such as sunrooms, outdoor living areas, or additional bedrooms can render the existing setup obsolete. Retrofitting an undersized system into a larger footprint typically requires duct alterations, electrical upgrades, and sometimes relocation of the outdoor unit. Designing with expansion in mind minimises future disruption and extra expenditure.
Overlooking Insulation Improvements
Upgrading insulation, glazing, or sealing gaps reduces the thermal load, potentially allowing a smaller unit to meet performance targets. Conversely, ignoring the benefits of improved building shell tightness may result in unnecessary oversizing. Integrating building-envelope upgrades with capacity decisions delivers both energy-saving and cost-optimisation advantages.
Discounting Technology Advances
Rapid innovation in compressor technology, refrigerants, and control systems can render yesterday’s equipment inefficient or obsolete. Investing in modular or scalable options facilitates technology refresh without a full system tear-out. Awareness of emerging solutions ensures that the installed capacity remains efficient and adaptable to new standards.
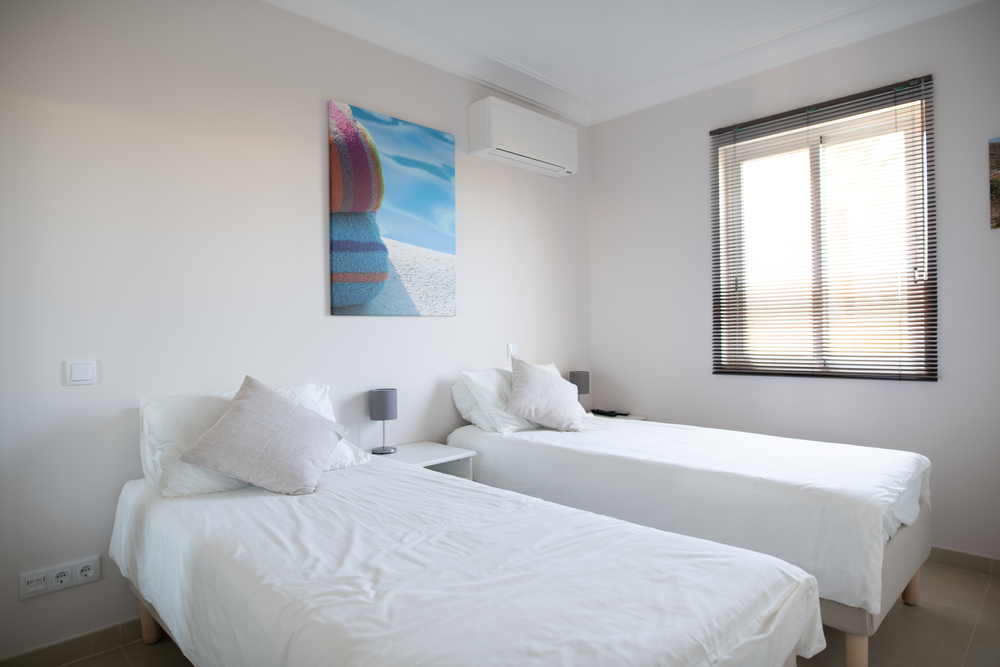
Poor Placement of Indoor or Outdoor Units
Even correctly sized equipment can underperform if positioned without due care. Optimal siting enhances airflow, minimises noise transfer, and guards against environmental stressors such as direct sun or salt-laden breezes. A strategic location fosters a balanced distribution of conditioned air and prolongs the lifespan of key components.
Incorrect Indoor Unit Location
Positioning the internal air-delivery unit too close to heat sources, obstructions, or busy living spaces undermines its ability to circulate treated air effectively. Placement decisions must balance aesthetic considerations with functional requirements for air intake and delivery. Attention to distance from electronics, lighting, and furnishings ensures consistent temperature control without unwanted drafts or noise intrusion.
Proximity to Heat-Generating Appliances
Locating the unit near cooktops, televisions, or other heat-emitting devices skews thermostat readings, causing the system to underperform. The internal sensor may detect artificially high temperatures and cycle excessively, failing to cool the occupied space properly. Over time, this mismatch leads to uneven comfort and possible overheating of electronics.
Installation Near Obstructive Décor
Heavy curtains, bookcases, or large furniture items placed in front of vents restrict airflow and create turbulence in the ductwork. Blocked flow increases static pressure, reducing the delivery volume to other rooms and forcing the blower to operate at higher speeds. Both energy consumption and noise levels can spike as the fan labours to overcome the obstruction.
Close Proximity to Occupied Areas
Placing indoor units directly above seating or sleeping areas may cause uncomfortable drafts, particularly during cooler weather. Occupants may feel cold blasts even when the overall room temperature is within range, prompting manual adjustments that further destabilise the system. Positioning the unit for gentle air diffusion balances comfort with efficient coverage.
Insufficient Clearance for Maintenance
Crowding the internal unit into tight alcoves or behind fixed cabinetry complicates filter access and coil cleaning. Neglecting routine servicing due to access issues accelerates component fouling and reduces heat-exchange efficiency. Ensuring at least the manufacturer-recommended clearance enables safe, timely maintenance and preserves performance.
Improper Outdoor Unit Siting
The outdoor condenser unit demands a location that supports ventilation, protects against environmental hazards, and facilitates ease of service. Poor siting risks debris accumulation, corrosion, and noise complaints while also limiting the unit’s ability to dissipate heat effectively. Strategic placement preserves both efficiency and aesthetic harmony with the property.
Exposure to Direct Sunlight
Positioning the condenser under prolonged sun accelerates refrigerant pressure rise and forces the compressor to work harder. Elevated operating temperatures reduce thermal exchange efficiency, increasing energy consumption and internal stress. Providing partial shade without obstructing airflow optimises performance and prevents overheating.
Inadequate Clearance Around the Unit
Walls, fences, or landscaping that encroach on the condenser restrict airflow and trap heat, leading to diminished cooling capacity. HVAC systems require unobstructed space—typically at least half a metre on all sides—for proper ventilation. Adhering to these guidelines helps maintain the intended energy-efficiency rating and prolongs component life.
Placement Near Salt-Laden Breezes
On a coastal strip, bunkering the condenser in an open area subject to salt spray can accelerate the corrosion of coils and mounting hardware. Salt deposits on refrigerant lines and fins impede heat transfer, compounding wear rates. Selecting a site with natural windbreaks and regular gentle rinsing minimises corrosive impact.
Poor Access to Servicing
Situating the outdoor section behind heavy shrubbery or tight fencing makes routine inspections and coil cleaning burdensome. Restricted access discourages homeowners from booking preventive maintenance, allowing dust and pollen to collect unchecked. Positioning the unit with clear, level access paths improves serviceability and long-term reliability.
Ignoring Local Climate Conditions
Each coastal region presents distinct environmental factors—humidity, salt air, prevailing winds, and temperature swings—that influence equipment performance and longevity. Designing an installation without regard for local weather patterns invites unanticipated degradation and efficiency losses. Integrating climate-specific considerations at the planning stage optimises both comfort and durability.
Underestimating Humidity Challenges
High ambient moisture slows moisture removal and can encourage mould growth within the ductwork. Systems must be capable of running longer dehumidification cycles without incurring a penalty on wear rates. Selecting equipment with robust moisture-handling capabilities ensures indoor air quality remains high.
Overlooking Prevailing Wind Directions
Wind-driven debris and salt spray can be channelled directly into the condenser if improperly oriented. Determining the typical wind patterns around the property guides the placement of windbreaks or protective screens. Anticipating these forces reduces the frequency of cleanup operations and corrosion mitigation tasks.
Neglecting Seasonal Temperature Extremes
A system optimised for summer may struggle during unseasonably hot or cool intervals without proper design allowances. Equipment controls and component ratings should accommodate the full annual temperature range, preventing compressor short-cycling or freeze-ups. A balanced configuration avoids reactive modifications that upset performance.
Discounting Rain and Storm Exposure
Coastal storms can deliver heavy rainfall and airborne debris capable of damaging delicate fins and fans. Raising the condenser on a sturdy, level platform and incorporating splash guards protects against water ingress. Planning for extreme weather events preserves both functionality and warranty validity.
Blocking or Closing Vents in Ducted Systems
Limiting airflow by sealing or obstructing vents might seem like an easy way to direct cooled air to occupied spaces, but it disrupts duct-static pressure, undermining system balance and efficiency. Proper airflow management depends on designed pathways that ensure even distribution and return-air circulation. Understanding the role each vent plays prevents well-intentioned but harmful modifications.
Disrupting Airflow Balance
Adjusting vent positions or permanently closing outlets in an attempt to concentrate airflow in certain areas upsets the calibrated equilibrium of a ducted network. The resulting pressure imbalances force blowers to operate beyond optimal ranges, causing noise increases and reduced delivery to distant zones. Restoring balance involves respecting the original airflow design and addressing underlying comfort issues.
Restricting Multiple Supply Outlets
When several vents are closed simultaneously, the system faces excessive static pressure, which may trigger safety cutouts. The fan motor endures added strain, risking premature burnout and potential bearing failures. Instead of permanently sealing outlets, consider adjustable louvres or zone-control dampers designed for balanced airflow management.
Overpressurising Certain Zones
Redirecting all conditioned air to one or two rooms may create pressurised areas that leak through windows and doors. Reduced overall airflow can then starve other parts of the home, leading occupants to open vents or tamper with dampers further. A zoned control system with dedicated thermostats offers a more effective solution than ad hoc vent closures.
Increasing Energy Use
As the blower works against higher resistance, it draws more current to maintain flow, eroding the benefits of variable-speed fans. Energy consumption spikes during high static-pressure conditions, directly impacting electricity bills. Regularly cleaning ducts and commissioning the blower curve helps restore design-level performance.
Accelerating Duct and Component Wear
High-pressure operation shortens the life of flexible connectors, seals, and dampers, leading to air leaks and noise infiltration. Over time, vibrations from the stressed fan assembly can loosen fasteners and degrade insulation around ducts. Maintaining vents in their original state preserves both airflow integrity and component longevity.
Neglecting Return Air Vents
The return-air side of the system is just as critical as the supply outlets; blocking or ignoring return grills disrupts airflow loops and can lead to negative pressure in living spaces. A well-maintained return path ensures air is drawn efficiently back to the unit for reconditioning and stabilising temperature and humidity levels throughout the cycle.
Covering Return Grilles
Placing furniture, carpets, or decorative screens over return vents effectively halts air intake, causing uneven cooling and elevated noise as the unit labours. Without adequate return flow, supply fans struggle to push conditioned air into the home, undermining system efficiency. Ensuring return outlets remain clear supports balanced circulation.
Installing Undersized Return Openings
Original return-air components may be too small for system upgrades, restricting volume and leading to high-velocity flow that creates whistling noises. Retrofitting larger or additional return grills alleviates airflow bottlenecks and reduces blower stress. A professional assessment of return-air capacity aids in achieving optimal balance.
Skipping Return-Air Filtration
Omitting filters at return slots allows dust and debris to circulate freely, coating coils and reducing heat-transfer efficiency. Dirty coils require more power to achieve the same level of cooling and can harbour microbial growth. Regular filter replacement and proper return-air filtration preserve indoor air quality and system performance.
Ignoring Pressure Differentials
Excessive negative pressure in rooms can pull in unconditioned outdoor air through gaps, undermining temperature stability. Measuring static pressure across return vents during commissioning verifies that the system operates within specified tolerances. Addressing duct leaks and resizing return components helps maintain balanced pressure.
Overlooking Vent Maintenance
Even properly sized and sited vents demand routine attention to ensure unobstructed airflow and hygienic operation. Accumulated dust, pet hair, and household debris can choke both supply and return outlets, eroding performance and affecting indoor air quality. Integrating vent cleaning into regular maintenance plans prevents degradation of comfort and efficiency.
Accumulated Dust on Supply Grilles
Visible dust layers on vent faces reduce the free area for airflow, forcing higher fan speeds to compensate. Indoor air patterns become disrupted, leading to uneven temperatures and potential hotspots. Wiping down grilles and vacuuming duct interiors alleviates pressure losses and maintains design-level performance.
Ignoring Flexible Duct Connections
Bends and joints in flex ductwork trap debris that eventually blocks airflow and compresses the duct, narrowing the passage. Compressed or collapsed ducts can cut supply volumes by more than half, severely impacting comfort. Periodic inspection and gentle straightening of flex ducts restore the proper cross-sectional area.
Skipping Damper Adjustments
Zone-control dampers can stick or misalign over time, restricting airflow to intended sectors. Small mechanical faults accumulate, leading to imbalanced distribution and unexplained comfort complaints. Exercising dampers regularly during maintenance checks ensures each zone receives its designed airflow share.
Neglecting Vent Filter Screens
Some supply vents include optional mesh screens to keep pests and large debris out of ducts. When left unwashed, screens block the airflow they were meant to protect. Monthly rinsing under low-pressure water flow keeps screens clear and prevents pest entry simultaneously.

DIY Repairs or Poor Installation
Attempting complex servicing tasks without proper training or ignoring manufacturer and statutory requirements can compromise safety, performance, and warranties. Every component in a modern cooling setup relies on precise calibrations and proven procedures that only qualified technicians can guarantee. Recognising one’s limits and engaging licenced professionals protects both occupants and equipment.
Attempting Complex Repairs Without Training
Fault diagnosis and component replacement are inherently technical activities that require specialised tools, refrigerant-handling certification, and electrical expertise. Homeowners lack the instrumentation to verify the refrigerant charge, circuit continuity, or control board parameters. Mistakes at this level can lead to irreversible damage and serious safety hazards.
Incorrect Refrigerant Charge Levels
Adding or withdrawing refrigerant without gauges and superheat/subcooling calculations risks both overcharging and undercharging. Imbalanced refrigerant volumes reduce cooling efficiency and can cause high-pressure shutdowns or compressor slugging. Only certified technicians should handle refrigerants to ensure correct operating pressures and environmental compliance.
Improper Wiring Connections
Mismatched wire gauges, poor terminations, or incorrect control board configurations can trip circuit breakers, damage electronic modules, or cause fire risks. Safe, code-compliant electrical work demands an understanding of load calculations and earthing requirements. Engaging a licenced electrician for any wiring work preserves system integrity and occupant safety.
Uncalibrated Thermostat Installation
Installing or relocating temperature sensors without recalibrating the control algorithm leads to inaccurate readings and erratic cycling. The thermostat head must be level and mounted away from heat sources or drafts. Failure to follow precise manufacturer guidance often invalidates warranties and triggers phantom faults.
Unsafe High-Voltage Handling
Accessing compressor terminals or fan-motor connections exposes individuals to lethal voltages. Even with the power isolated, residual charge on capacitors and control boards can deliver dangerous shocks. Professional servicing guarantees proper discharge procedures and lockout/tagout protocols.
Using Incorrect or Low-Quality Parts
Substituting original components with generic or mismatched alternatives may save money upfront but can lead to performance losses, reduced durability, and voided warranties. Every part—from capacitors to expansion valves—is engineered to work harmoniously within the system’s operating envelope. Compromising on quality undermines the entire installation.
Non-OEM Filters and Components
Off-brand filter elements often fail to meet micron-capture specifications, allowing dust and allergens to penetrate coil surfaces. Generic capacitors and relays may lack the thermal tolerance or electrical characteristics required, leading to early failure. Specifying approved parts maintains design-rated efficiency and longevity.
Incompatible Refrigerant Substitutes
Filling a system designed for one refrigerant type with another without necessary component changes can lead to pressure mismatches and lubrication issues. Mismatched viscosity and acid-resistance properties cause bearing wear and valve corrosion. Adhering to the original refrigerant specification safeguards both equipment and the environment.
Low-Grade Insulation Materials
Using substandard pipe wrapping or sealants on refrigerant lines and duct leaks results in condensation, energy loss, and potential water damage. Superior insulation keeps refrigerant at the intended temperature and prevents structural moisture issues. Investing in correct materials pays dividends in performance and protective efficacy.
Economical Wiring Accessories
Thin-walled conduit, improperly rated connectors, and low-quality cable ties can degrade under UV exposure or thermal cycling. Faded markings and brittle plastic lead to loose connections and electrical shorts. Applying professional-grade hardware ensures reliable, long-term operation.
Skipping Commissioning and Testing
After installation or service, thorough commissioning—load testing, leak detection, and performance verification—is crucial to confirm that the system meets design criteria. Bypassing these steps may allow hidden problems to persist, causing inefficiencies and potential breakdowns that surface months later. A documented handover process ensures that occupants, technicians, and warranty providers share a clear understanding of system status.
Neglecting Refrigerant Leak Checks
Even small leaks reduce cooling capacity and accelerate oil carryover into coils, leading to foam formation and blockage. Electronic leak detectors and pressure tests confirm system tightness before active operation. Early detection prevents gradual performance decay and environmental harm.
Omitting Electrical Safety Tests
Verifying insulation resistance, earth continuity, and correct breaker coordination prevents fire hazards and nuisance tripping. Thermal imaging scans of wiring harnesses and motor windings can uncover hot spots before they fail. A comprehensive safety certificate assures occupants of risk-free operation.
Forgoing Airflow Measurements
Measuring static pressure and volumetric flow rates across coils validates that duct design matches blower performance. Under- or over-ventilation can both induce comfort issues and energy wastage. Balancing dampers and adjusting fan curves during commissioning preserves design-level airflow.
Skipping Performance Documentation
Recording baseline metrics—power draw, temperature differentials, and cycle durations—provides valuable reference points for future maintenance. Without these data, technicians cannot assess system degradation accurately over time. Proper documentation enhances both service efficiency and warranty claims.
By recognising these common missteps—improper sizing, misplaced units, obstructed airflow, and unauthorised repairs—homeowners can make informed choices at every stage of selecting, installing, and maintaining their cooling solutions. Investing time in accurate load calculations and future-proofing capacity ensures the system operates efficiently under both current and evolving needs. Thoughtful placement of indoor and outdoor units minimises noise and environmental stress while maximising airflow and ease of maintenance. Preserving designed duct pathways and keeping vents and returns unobstructed not only balances temperature distribution but also extends the lifespan of critical components.
We Run Our Business Like a Family
When You Need Help
Get your home the Air Conditioning work it needs from our team at All Coast Air Conditioning. We’re always ready to help.